Fused Deposition Modeling
The Fused Deposition Modeling (FDM Printing) process forms three-dimensional objects on an FDM machine from CAD-generated solid or surface models. A temperature-controlled head extrudes thermoplastic material layer by layer. The rapid prototype emerges from the FDM 3D printer as a solid three-dimensional part without the need for tooling.
- The FDM Printing process begins with the design of a rapid prototype model on a CAD workstation
- The design is imported into a program that mathematically slices the rapid prototype model into horizontal layers
- Another piece of software is used to generate the supports as required.
The FDM 3D Printer system operates in the X, Y and Z axis. In effect, it draws the model one layer at a time on the FDM printer.
Our Fortus FDM printing technology, a Stratasys branded FDM printer was developed with input from the Aerospace market to focus on being able to build end-use, production quality 3D printed parts with costs comparable or cheaper than other 3D printing processes.
FDM printing can perform exceedingly well under a wide temperature range, undergo rigorous testing and have long term shelf life. Several Fortus materials are able to be sterilized using an autoclave, making it ideal for medical applications and that same high temperature threshold also makes it possible to use the parts for under hood applications in automotive testing. For production line work, the durability makes fused deposition modeling ideal for jigs and fixtures.
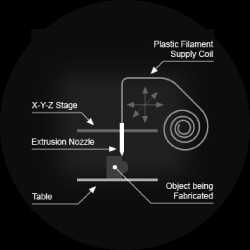